Tecnica – Il DPV: l’anti-lag secondo i francesi al tempo del Gruppo B
Scopriamo insieme il sistema adottato da Peugeot e Renault per annullare il ritardo nella risposta del turbo
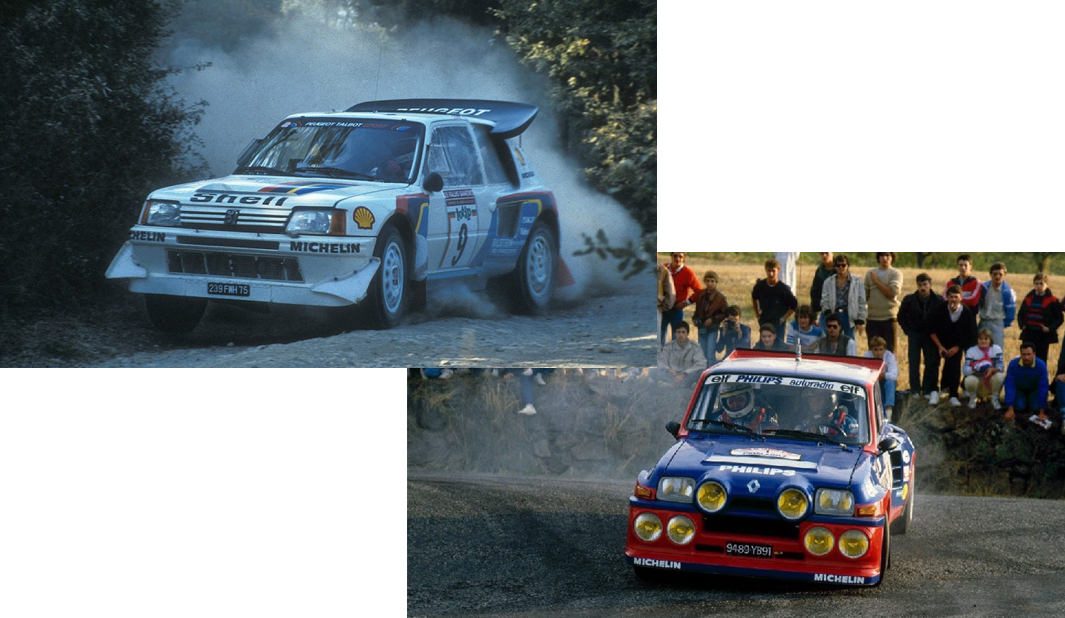
Di “Rivoluzioni” la storia ne è piena, e anche senza scomodare il campo politico non si fatica di certo a trovarle anche sul nostro terreno di caccia preferito: il motorsport. Le prime auto a motore posteriore (eh sì Commendatore…alla fine i buoi son finiti dietro al carro), l’introduzione delle prime ali a scopi aerodinamici, l’effetto suolo, il turbo. Già, il turbo. Massima espressione della volontà dell’uomo di “andare sempre più forte e più in alto”.
Come al solito è l’industria aeronautica ad aprire la strada, con l’automobile sempre lì, pronta a carpire ogni segreto per migliorarsi anch’essa. Agli americani va il merito di aver aperto la strada, con il turbo che già a fine anni ’60 è vittorioso sull’ovale più famoso del mondo. Dopo Indy tocca alla Can-Am essere travolta, nel 1972, dalla Porsche 917/10 e da suoi 850 cavalli sovralimentati. In Formula 1 ci vuole più tempo e bisognerà aspettare il 1977 e i francesi per vedere un motore turbo esordire nel campionato più famoso del mondo, e altri due anni per vederlo cogliere la prima vittoria, sempre grazie a Renault. Quasi in contemporanea è invece la Saab a firmare la prima vittoria del turbo nei rally, sempre nel ’79, anticamera del ciclone Quattro che arriverà da Ingolstadt qualche anno dopo.
Sembra tutto bello: potenze infinite con cilindrate irrisorie, motori piccoli e leggeri, ma i problemi sono solo dietro l’angolo, in attesa. Oltre agli iniziali problemi di affidabilità il turbo presenta infatti un problema intrinseco: La risposta ai bassi regimi. In Renault si rendono conto che la loro RS01 in uscita dalle curve lente è semplicemente ferma. Alzando il piede dal gas infatti, il pilota toglie semplicemente l’alimentazione alla turbina, visto che di fatto riduce la portata dei gas di scarico che trascinano la componente calda del turbo. Il compressore quindi ruota anch’esso ad una velocità bassa, troppo bassa, e diventa un tappo per l’aspirazione del motore. Nel momento in cui il pilota torna a chiedere potenza pestando sul gas la turbina impiega del tempo per tornare ad un regime di rotazione accettabile, e permettere quindi al compressore a lei collegato di fornire la pressione necessaria. Si tratta di attimi, certo, ma sufficienti per dare la sensazione al pilota di essere alla guida di un’Ape diesel. Signore e signori ecco a voi il famigerato “turbo-lag”.
Il DPV nei rally
Per risolvere il problema il team di Jean Pierre Boudy, il mago dei motori F1 Renault, ha una geniale intuizione. Se in casa Lancia qualche anno dopo la soluzione al problema prenderà la forma della doppia sovralimentazione, in casa Renault si concentrano su una soluzione che, seppur forse meno efficace, è sicuramente più semplice. Il risultato è il Dispositif Pre-rotation Variable, abbreviato in DPV.
Il DPV fu introdotto e sviluppato come detto da Renault per risolvere le problematiche sui suoi motori di Formula 1, ma nel gennaio del 1984 Jean Pierre Boudy cambiò casacca, e passò alla Peugeot. Questo permise alla casa del leone rampante di attingere alle conoscenze di Boudy e di sviluppare quindi un proprio sistema DPV.
Il risultato fu che proprio Peugeot ebbe l’opportunità di far debuttare il sistema nei rally con la 205 T16, bruciando così sul tempo i cugini. Renault infatti implementerà la soluzione solo sulla versione Maxi Turbo della sua R5, il cui debutto fu successivo a quello della Peugeot 205 T16.
Dispositif Pre-rotation Variable (DPV): come è fatto
Vediamo ora insieme nel dettaglio come è fatto e come funziona il DPV aiutandoci con un disegno proveniente direttamente dal brevetto Renault numero 4471616:
Alla bocca di ingresso del compressore viene abbinato un dispositivo (32) che ha il compito di variare la sezione di passaggio dell’aria aspirata e anche la direzione del flusso stesso. Il dispositivo è composto da una serie di palette (33) disposte radialmente lungo la bocca di aspirazione (34), che possono ruotare ognuna sul proprio asse (35). Le palette possono essere messe tutte in rotazione contemporaneamente dall’anello (36). Questo anello è messo a sua volta in rotazione dalla bielletta (43), che fa parte del cilindro (37). In questo video potete vedere bene la bielletta (43) che mette in rotazione il disco (36).
Nel sistema descritto a brevetto il cilindro (38) è collegato direttamente all’acceleratore (28) tramite il braccio (39). La camera interna di questo cilindro è invece messa in comunicazione (tramite 42) direttamente con il condotto di aspirazione a valle delle valvole a farfalla (25). All’interno del cilindro è presente un pistone (41) e una molla (44) che viene caricata e spinta dal pistone sotto l’azione dalla pressione presente in camera (40), ovvero quella all’aspirazione. In questo modo l’azione sull’anello (36) è una combinazione delle azioni date dal pedale dell’acceleratore e dalla pressione nel condotto di aspirazione.
È poi presente un sistema di regolazione (19) composto da due camere (20 e 21), separate ermeticamente da un pistone con tenuta (22) e tenuto in posizione da una molla precaricata (24). La molla è collegata ad un altro elemento scorrevole all’interno della camera (20) e questa camera “sente” la pressione a valle del compressore tramite il condotto (20a). Il pistone (22) è collegato ad una valvola (17) tramite l’elemento (23). La valvola (17) ha sede (18) nel condotto di scarico a monte della turbina (6).
È vero: avevamo detto che era semplice,
DPV: come funziona
A pieno carico, con il pedale dell’acceleratore a fondo sulla lamiera, tutto funziona come un normale motore turbo compresso. Il cilindro (38) è spinto per intero dall’acceleratore e anche la pressione in camera (40) spinge al massimo il pistone (41) che comprime la molla (44). Questo perchè è massima la pressione di aspirazione dopo le valvole (25) per effetto dell’azione del compressore. Il risultato è che la bielletta (38) spinge anch’essa completamente sull’anello (36) del DPV, che ruotando posiziona le palette nella posizione di massima apertura. In figura 1 sotto possiamo vedere schematizzata la situazione: nella sezione a sinistra vediamo le palette (33), disposte radialmente in posizione di massima apertura, che non modificano la direzione dei flussi aspirati, i quali vengono incanalati normalmente verso il compressore (figura a destra).
Se la pressione nel condotto (16) a valle del compressore dovesse salire troppo, per proteggere il motore dobbiamo stabilizzare la pressione di sovralimentazione e per farlo dobbiamo stabilizzare la velocità di rotazione della turbina. Nel nostro caso entra in azione il sistema di regolazione (19). La pressione di aspirazione nel condotto (16) e trasmessa alla camera (20) tramite (20a), fa muovere l’elemento all’interno della camera che a sua volta “tira” la molla (24). Oltre un certo valore di precarico la molla richiama il pistone (22) e di conseguenza la valvola (17) che esce dalla sua sede (18). Così facendo si crea un bypass dei gas di scarico verso il condotto (9a) che non vengono quindi processati dalla turbina. Quest’ultima non aumenta ulteriormente il suo regime di rotazione e di conseguenza stabilizza anche la rotazione del compressore, e quindi la pressione di sovralimentazione. Il tutto agisce e funziona come una wastegate.
Vediamo ora cosa succede invece nella fasi di rilascio, dove il sistema ha il suo vero utilizzo. Appena il pilota toglie il piede dal gas il solito cilindro (38) viene richiamato e così facendo l’anello (36) mette in rotazione le palette. In aggiunta la chiusura delle valvole a farfalla (25) fa calare la pressione in camera (40). La molla spinge indietro il pistone che così richiama la bielletta (43) e questa fa muovere ulteriormente l’anello e quindi le palette. Ora siamo nel caso in cui il DPV è nella modalità “tutto chiuso”. Le palette si trovano ora in una posizione per cui l’aria che vien aspirata (il motore continua a “respirare” anche in rilascio) viene messa in rotazione dalla posizione delle palette e dall’area di passaggio rimasta (come in figura 2 sotto).
Ecco perchè il dispositivo è detto di “pre-rotation”. La rotazione innescata è nel senso di rotazione del compressore, che quindi viene adesso spinto dall’aria in rotazione. In questo modo il compressore agisce quasi come una turbina e non consuma più la potenza di cui necessitava per svolgere la sua funzione di accelerare l’aria al suo ingresso. Il compressore non sta ora svolgendo la sua funzione, ma non sta nemmeno perdendo velocità (o almeno sta rallentando in maniera molto ridotta), che è quello che interessa in questa fase. Un altro effetto positivo di far lavorare il compressore come una turbina è l’ulteriore calo di pressione all’aspirazione, che porta a frenare il motore ulteriormente. Quasi come un freno motore aggiuntivo.
Nel momento in cui il pilota torna sul gas il cilindro (38) torna ad essere spinto in avanti, ma le palette non vengono messe in posizione “tutto aperto” bensì in una posizione intermedia. Manca infatti il contributo della pressione in camera (40), perchè la pressione all’aspirazione è ancora bassa (abbiamo appena aperto il gas). In questo modo si mantiene una componente con effetto rotativo sul compressore, ma comincia ad aumentare leggermente l’area di passaggio per preparare il compressore alla fase successiva. Ci troviamo nella zona (45) del grafico in figura sotto: la pressione di sovralimentazione è costante e le palette sono inclinate di 30° circa.
La turbina sta però via via accelerando ulteriormente sotto la spinta dei gas di scarico e il compressore riprende velocemente la poca velocità che aveva perso e ricomincia ad assorbire potenza e a generare pressione all’aspirazione. L’aumento di pressione è repentino e questo non fa altro che spingere ulteriormente la bielletta (43) che fa ruotare ancora le palette. Siamo ora nella zona (46) del grafico dove aumenta gradualmente sia la pressione di sovralimentazione sia l’inclinazione delle palette. La pressione aumenta in maniera controllata e non in maniera brusca rendendo il motore molto più guidabile. Il tutto fino a riportarsi alle condizioni “tutto aperto” e quindi di massima spinta.
Tutto questo si traduce in una immediata risposta del motore a qualsiasi regime di rotazione. Questo perché non viene mai permesso al compressore di rallentare troppo, il tutto grazie alla pre rotazione impressa all’aria aspirata durante le fasi di chiusura del gas. Il DPV fa sentire la sua forza soprattutto nelle fasi transitorie, in cui magari stiamo viaggiando a gas non completamente aperto ma neanche in totale rilascio. La posizione delle palette sarà infatti intermedia, e questo fornirà sempre una componente di rotazione all’aria che permetterà al compressore di girare ad una velocità superiore rispetto al suo reale fabbisogno in quell’istante, ma che ci permetterà una risposta istantanea quando si tornerà a schiacciare il pedale a fondo.
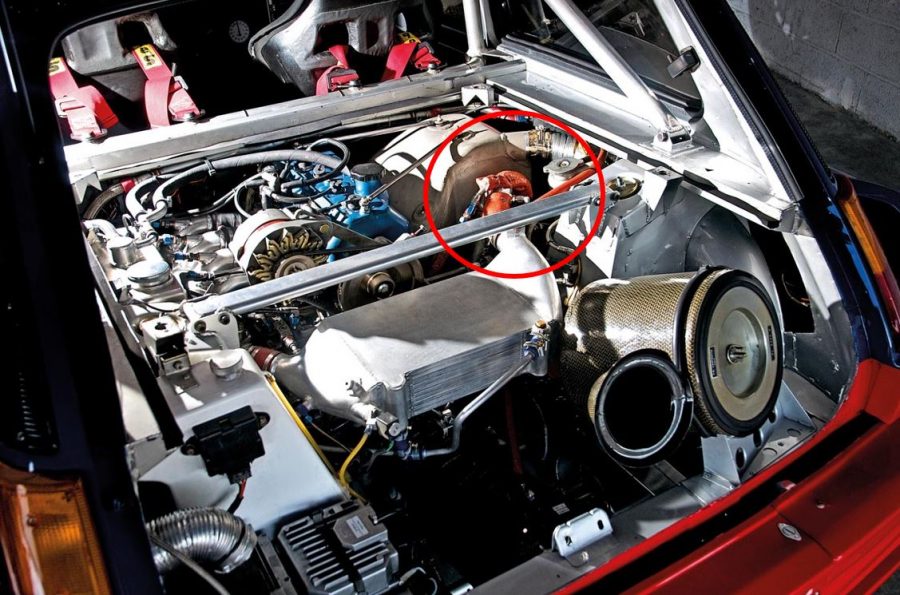
Una ultima cosa da segnalare è l’assenza della valvola pop-off in quanto non è più necessaria. Quando si chiude il gas infatti la repentina chiusura delle palette che innesca la rotazione dell’aria aspirata fa si che il compressore smetta immediatamente di comprimere l’aria stessa, ma si limiti ad essere trascinato. Questo impedisce automaticamente il verificarsi di qualsiasi “effetto martello” sulle valvole che rendeva necessario l’utilizzo della pop-off per sfiatare la pressione in eccesso.
Tra le debolezze del sistema c’è sicuramente la difficoltà nella taratura del tutto e il costo, che non lo rendono implementabile sulle vetture di serie. Un altro incredibile vantaggio invece è che non presenta dispositivi mobili all’ingresso in turbina dove i gas caldi dello scarico mettono a dura prova la resistenza dei materiali.
2 Comments
Giuseppe
Articoli tecnici come queso del DPV sono molto appassionanti,grazie.
Andrea Carraro
Grazie Giuseppe! E non ci fermeremo qui